APIs have become the go-to solution for container tracking, promising automation and real-time visibility. But as Terminal49’s Matt Turner pointed out in our fireside chat:
“APIs are just pipes—they deliver the data, but if the data itself is wrong, incomplete, or delayed, the API isn’t going to help much.”
That’s the real issue. APIs only move data from one place to another. If the information coming from ocean carriers and terminals is inaccurate or missing key milestones, then even the best API can’t fix the problem.
This blog builds on our fireside chat discussion to explain why data quality—not just API access—determines whether you can reliably track containers and make smart logistics decisions.
The Data Problem: Bad Inputs = Bad Outputs
Every shipper, freight forwarder, and logistics provider has experienced it: You pull up container tracking data, only to find it’s missing key events or showing outdated timestamps. You refresh the page, try a different carrier portal, maybe even pick up the phone to verify what’s actually happening.
Why does this keep happening? The problem starts at the source. APIs only reflect the data carriers and terminals feed into them. And that data pipeline is far from perfect.
1. Missing Events: Critical Milestones Are Often Skipped
In our fireside chat, Terminal49 CEO Akshay Dodeja shared a frustrating but common example:
“We’ve seen carriers skip key milestones like ‘vessel loaded’ altogether. That leaves shippers guessing.”
This is a big deal. Without a "vessel loaded" confirmation, a shipper has no way of knowing whether their container actually made it onto the intended vessel—or if it’s still sitting at the terminal due to a delay. That’s not just an inconvenience; it’s a major disruption to supply chain planning.
2. Inconsistent Data Quality Across Carriers and Terminals
Not all carriers and terminals operate with the same level of digital sophistication. Some terminals have fully automated tracking systems that instantly update container movements, while others still rely on manual data entry. That means:
- Some carriers report detailed timestamps, while others only update milestones once or twice a day.
- Different systems might use varying definitions for the same event—what one carrier calls “vessel departure,” another might classify differently.
- Some carriers include customs clearance and release statuses, while others provide only the basics.
When you’re tracking hundreds (or thousands) of containers across multiple carriers, these inconsistencies make it nearly impossible to maintain a clean, accurate picture of what’s happening.
3. Delays in Updates: The Data You See Is Already Outdated
Even with modern automation, not all tracking updates happen in real-time. As Matt explained:
“You can have three carriers, all using the DCSA API, all following the spec exactly, and still see different data quality, different timeliness, and different completeness of events.”
This delay can be caused by several factors:
- Terminal systems that don’t sync instantly with carrier databases.
- Data transmission lags between different supply chain stakeholders.
- Manual validation processes that slow down updates.
The result? By the time you see a tracking event, your container may have already moved to a different stage—leaving you constantly behind.
Why Bad Data Costs You More Than You Think
In our fireside chat, Akshay used a relatable analogy to drive the point home:
“Imagine tracking your food delivery. If the app says it’s 10 minutes away, but you check again and it’s 30 minutes, you’re frustrated. Now imagine that frustration, but it’s a $200 demurrage fee instead of dinner.”
Tracking isn’t just about visibility—it’s about avoiding costly mistakes. When data is unreliable, businesses suffer.
1. Higher Costs: Bad Data Leads to Demurrage, Per Diem, and Storage Fees
One of the biggest financial risks in container logistics is poor visibility leading to unexpected fees. If you don’t know when a container is available for pickup, you might miss your free time window—racking up hundreds or thousands of dollars in demurrage and per diem charges.
Let’s say a port updates your container status at 8 AM, but you don’t receive that data until later in the afternoon. If your trucker misses the pickup because of that delay, you could end up paying an extra day’s worth of fees. Multiply that by dozens of containers, and the costs spiral fast.
2. Wasted Time: Chasing Down Missing Data
How much time does your team spend manually checking carrier websites, making calls, and digging through spreadsheets to verify container status? Every time a tracking event is missing or inaccurate, someone has to step in and fix the issue—draining hours from your operations team.
3. Operational Chaos: Delayed Data Disrupts Trucking and Warehousing
If you don’t have reliable ETAs, how do you plan drayage pickups? How do you coordinate warehouse staffing and inventory movement?
Unreliable tracking data leads to a chain reaction of inefficiencies:
- Trucks arrive too early or too late, increasing wait times and detention fees.
- Warehouses don’t know when to prepare for inbound shipments.
- Customer service teams struggle to provide accurate updates, leading to frustrated clients.
A single bad data point can disrupt the entire supply chain.
How Terminal49 Fixes Data Chaos
At Terminal49, we know that access to data isn’t enough—you need data you can trust. That’s why we’ve built our platform to not just aggregate data, but to clean, validate, and enrich it so you always get the most accurate and up-to-date information.
1. Multi-Source Data Validation
We don’t just take carrier data at face value. Terminal49 cross-references tracking information from multiple sources—including ocean carriers, terminal operators, and proprietary datasets—to identify inconsistencies and fill in missing milestones.
2. Real-Time Updates with Push Notifications
Unlike traditional tracking systems that require constant manual checks, Terminal49 delivers automatic updates the moment a new event is recorded. That means you’re always working with the latest available data—without having to refresh a webpage every five minutes.
3. Seamless API and Dashboard Integration
Whether you want to integrate tracking data into your TMS, ERP, or other logistics software, or just need a user-friendly dashboard for quick access, Terminal49 makes it easy. We turn raw data into actionable insights, helping you make better decisions, faster.
Learn more about how Terminal49 ensures data quality here.
Watch the Chat for More
Want to hear the full discussion on why data quality is the missing piece in container tracking? Check out this clip from our fireside chat:
APIs Alone Won’t Fix Container Tracking—Reliable Data Will
As Akshay said in the chat:
“Accessing data is one thing. Getting data that’s reliable, timely, and complete is where the real value is.”
APIs can provide access, but without high-quality data, they won’t solve the core issues in container tracking. That’s why Terminal49 goes beyond simple API aggregation—we ensure the data you rely on is accurate, complete, and actionable.
Ready to stop making decisions based off bad container milestones?
Let’s talk about how Terminal49 can simplify your container tracking.
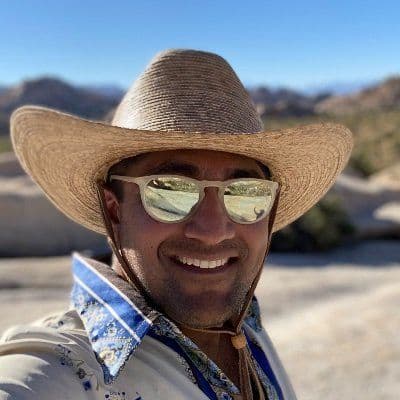