Construction timelines can be stringent, so much so that the construction industry relies on precise timing and seamless delivery of materials and equipment for businesses to meet deadlines. However, less than 10% of projects are completed on time. The problem is that any delay can cripple the entire construction project, triggering a ripple effect of challenges that have serious consequences on the budget and timelines of the project. The importation of cement, artificial stones, and other construction materials reached $2.7 billion in the United States. However, when delays are introduced into the process, they can ultimately impact customer satisfaction and the profitability of the construction business.
The cascading effect of delays in the construction process can be a serious challenge for stakeholders, but these delays also begin long before the shovels hit the ground. Addressing them begins with the entire supply chain and its ability to deliver on time. Construction professionals rely on transparent supply chains to maintain the efficiency and reputation of companies in the sector, impacting timelines and ensuring material availability. Terminal49 can enhance the visibility and transparency of these solutions (including proactive alerts and accurate ETAs), which will be discussed in detail in this article. Furthermore, the article explores the consequences of delays and the common causes.
The High Cost of Construction Delays
Construction delays are a menace, whether you're a small or medium-sized enterprise (SME) or a large importer of construction equipment. When construction projects are delayed due to resource unavailability, timelines are extended, and the construction team is restricted from taking on new ventures. Keeping customers satisfied becomes an ongoing challenge. The constant back-and-forth communication and managing expectations can put immense pressure on customer success teams, often forcing importers and construction businesses alike to dip into reserves to maintain service levels and protect their reputations.
Construction delays from missing shipments, whether local or international, and late delivery of materials, such as cement, have two major consequences, and both come with high costs to the business.
1. Financial Impact
According to the Construction Industry Institute, delays are expensive and can average between 20% and 30% of a project's duration. For instance, a $100 million project could incur approximately $30 million in additional costs if shipping operations are delayed by 30%. For more context, this translates to about $45,662 per day in lost revenue during the delay period. The bottom line is that when construction projects are delayed, spending increases. Whether paying laborers to stay on-site or extending equipment rentals and permits because of delayed shipments, when construction shipments are not on time, it will surely be accompanied by increased expenses.
Depending on the nature of the contract, missed deadlines can also incur financial penalties. All these costs can quickly accumulate, jeopardizing profit margins. Revenue generation and loan servicing problems can also devastate importers. Whether for commercial property or public infrastructure meant for community use, delays can leave projects unfinished and income streams frozen. If loans were secured to fund the project, each passing day of the shipment delay would compound the financial burden. Worse yet, the strain can escalate into legal disputes as contractors, subcontractors, and clients demand accountability for setbacks, further draining resources and damaging relationships.
2. Operational Impact
The average construction project has a tightly coordinated schedule. One delay can disrupt the project team and processes, creating inefficiencies with dire consequences. For example, if the materials for a building's pillars are unavailable, the top floor cannot be built. Say the construction was timed to beat the weather before it became a problem. That project is no longer at the mercy of materials but the environment, creating new issues and delays.
Managing resources — such as labor and equipment — becomes significantly more challenging when plans are unpredictable. The transportation of these materials, whether local or international, trucking or container ships, can aid in these complications if not chosen or done correctly. Beyond immediate impacts, repeated shipment delays can harm an importer’s reputation. Clients and partners may lose confidence, affecting opportunities for future shipments and long-term relationships.
Impact of Material Delivery Delays on Construction Timelines
Materials are vital to construction, whether for a building, boat, or other project. They must be available at the right time to keep the construction project schedule on track. However, the transportation and logistics of getting these materials to the site are usually beyond the control of the engineers. In today’s world, delays could be for any reason, including geopolitics, trade wars, port congestion, or rising tariffs.
Shipment delays can quickly turn into major bottlenecks, particularly when updates are sparse or arrive too late to take corrective action. Late shipments from suppliers, unreliable ETAs, and a lack of visibility into shipment status can leave project managers scrambling to adjust timelines.
Take, for example, the beginning of the pandemic in early 2020, which led to widespread factory closures, particularly in China and Italy, which halted the production of essential materials like steel, concrete, and various components. The result was significant delays in ongoing and new construction projects across the U.S. as suppliers struggled to meet demand amid a backlog of orders.
The problem emphasized the need for tech-driven solutions like reliable and real-time tracking that ensured complete transparency for all stakeholders involved. That way, there is better planning and downstream construction projects do not have to expect shipments that cost the companies involved their reputation, money, and future businesses.
When logistics providers fail to communicate effectively or provide real-time tracking, anticipating and mitigating delays becomes nearly impossible. The result is wasted time, inefficient resource allocation, and frustrated stakeholders.
How Terminal49 Can Help Avoid Delays on Construction Timelines
Shipping in materials is not the problem. The real challenge is the lack of control and access to the necessary information, which stifles the ability to plan and schedule the construction process and other project tasks effectively. This has a much greater impact on the construction industry because of the high cost of goods, types of materials, and impact on the industry. However, that is where Terminal49 plays a key role. Terminal49 is a tracking platform that allows shippers unfettered access to information about their shipments.
For the construction industry and businesses, this means they can effectively plan their construction process to tally with the arrival of these shipments. Here are solutions that can be leveraged on the platform to help:
1. Access to Accurate Data
Terminal49 offers a centralized platform for tracking and managing container shipments, eliminating the need for manual updates and fragmented processes when shipping construction materials. With features like real-time milestone tracking, customizable reports, and instant alerts, shippers or other stakeholders can monitor container data to determine shipment statuses, address potential issues with the materials being shipped, and enhance the operational efficiency of the entire construction process, all from a single dashboard.
What to expect from the container tracking dashboard:
- Accurate Data: Up-to-date container information verified and standardized for reliability.
- Simple Setup: Track shipments by entering basic details like a container or booking number.
- Efficient Management: Tools to prioritize at-risk containers and streamline communication.
- Advanced Reporting: Tailored reports and visualized routing insights for better planning, especially when implementing the critical path method or other construction scheduling technique(s).
- Enhanced Collaboration: Share personalized dashboards with team members and clients.
2. Leveraging Technology for Real-Time Visibility
Terminal49 gives project managers complete visibility and transparency by providing real-time updates and proactive alerts. This allows them to anticipate potential disruptions and take corrective action before delays escalate.
1. Proactive Alerts
Terminal49's system notifies users of issues like port congestion, customs delays, or changes in vessel schedules. This early warning system helps construction teams prepare for potential setbacks and ensures they can adjust their plans promptly.
2. Accurate ETAs
Unlike the traditional methods that rely on broad estimates, Terminal49 delivers precise arrival times for shippers. This accuracy allows construction or project managers to coordinate resources effectively, reducing idle time and optimizing scheduling.
3. Enhanced Communication
Terminal49’s centralized tracking system improves collaboration by providing all parties with a shared view of shipment status. This transparency fosters better decision-making and reduces misunderstandings from the beginning of the construction process until project completion.
Wrap Up
The consequences of delays in construction and project timelines are far-reaching. However, they can be proactively addressed with a platform like Terminal49. This tech solution enhances shippers' ability to plan better, make smarter decisions, mitigate shipping delays, and collaborate more effectively through clear communication. Features like proactive alerts, accurate ETAs, and container tracking dashboards provide the construction team or business with the tools to avoid costly disruptions while ensuring efficiency, seamless inventory management, and a positive reputation across the construction industry. Schedule a demo today.
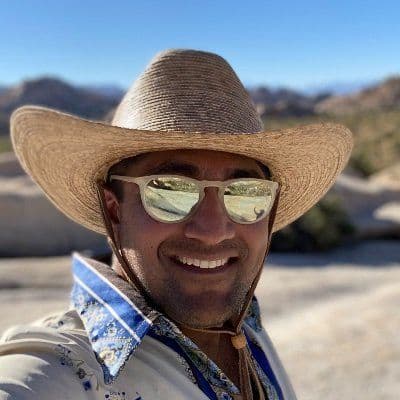